Overview
Through our transformer lifecycle management programme, we carry out a series of tests to offer the best possible performance of your transformer – enhancing its longevity and improving its reliability.
The programme is a combination of the services listed below and can be applied from the beginning of a transformer’s life, or when you feel changes may need to be made to your existing equipment.
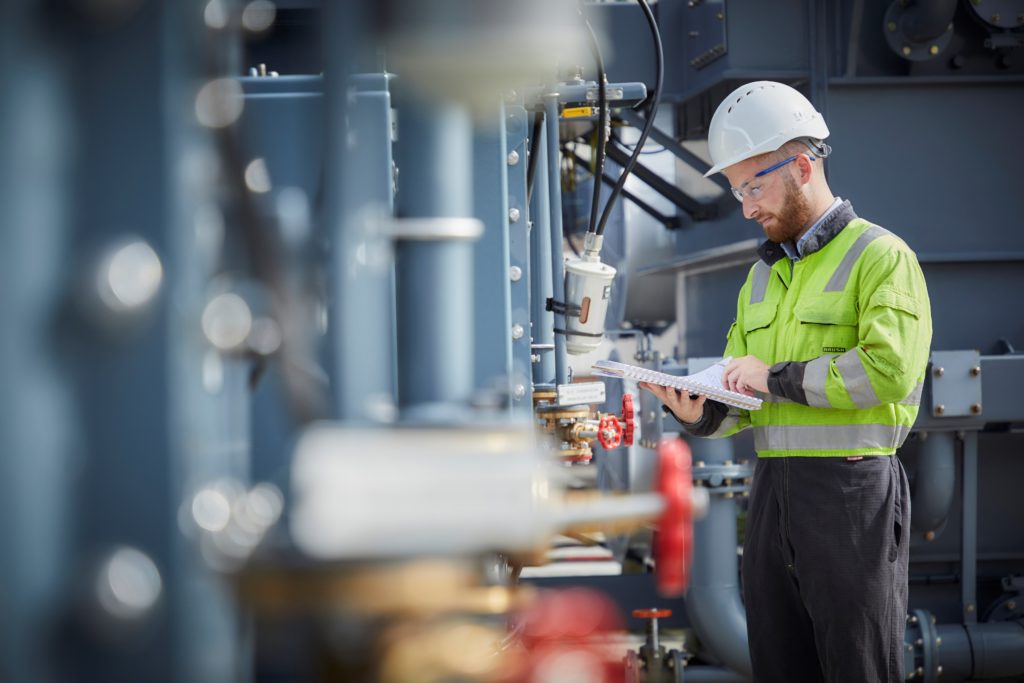
VIEW FROM THE TEAM
What are the typical advantages of transformer lifecycle management?
A lifecycle management programme gathers vital data on the condition of your transformer.
This information tells us about factors such as suspected transformer faults, condition assessment for network planning, details on condition pre/post relocation, confirmation of condition on delivery, transformer failure investigation and the plotting of degradation.
Capabilities
Transformer inspections and health checks
Preventative maintenance is the key focus of our lifecycle management programme. Available to all BRUSH transformer products and those of third parties, this comprehensive inspection scheme provides a continuous appraisal of your equipment’s current condition.
The benefit of regular inspections and checks is that potential problems can be found and addressed – before they become bigger issues. The programme can also be tailored to your operational needs, giving you control over aspects such as when to schedule the required equipment outage time needed for inspections to take place.
Transformer maintenance contracts
We believe prevention is better than cure, and we ensure your transformer is always functioning at its best by putting in place a fully-customised support package that’s right for your system and your business.
Ongoing maintenance gives advanced warning of your transformer’s deterioration, highlights high priority assets, reduces the risk of unexpected outages and provides proof of condition upon delivery. And because all previous results are kept on file, we’re uniquely placed to compare data and address issues before they become expensive, real problems.
Transformer testing and condition monitoring
We can carry out a series of crucial tests that help determine the condition of your transformer to see if it has been damaged or if it should even be removed from service. These tests are as follows:
SFRA (Sweep Frequency Response Analysis)
This is a reliable method of monitoring the physical condition of a transformer and its components. It can efficiently detect displacement of transformer cores, deformation of windings, faulty core grounds or broken and/or loose connections.
Capacitance and dissipation factor
Measuring capacitance and dissipation factor helps us determine the insulation condition between windings or within bushings.
Changes in capacitance can indicate mechanical displacements of windings or partial breakdown in bushings. Ageing and degradation of the insulation, together with the presence of moisture, increase the amount of energy that is converted to heat in the insulation. The rate of these losses is measured as dissipation factor.
Polarisation Index
Polarisation Index is used to indicate the condition of transformer insulation. It’s a ratio of the insulation resistance measured for 10 minutes to the insulation resistance value measured after one minute.
DFRA (Dielectric Frequency Response Analysis)
The dryness and condition of paper insulation is a key factor in both short and long-term power transformer reliability. DFRA testing is an excellent tool for diagnosing transformer insulation issues and is effective in assessing moisture in power transformers.
Winding resistance
Measuring a transformer’s DC winding resistance from one external terminal to another assures that the windings are intact, and the internal connections are correct. The resistance measurements also indicate there’s no severe mismatches or open circuits throughout the tapping range.
Dissolved gas analysis
When insulating oil is subjected to high thermal and electrical stress, gasses are generated from the decomposition of the oil. Different types of faults generate different gasses. Analysing these gasses tells us a lot about the condition of your transformer.
Transformer oil analysis
By studying the oil in your transformer, we can monitor the health of your system and identify ways to optimise its performance. The testing and analysis of the samples also lets us highlight and fix issues that could lead to costly shutdowns or repairs if left unresolved.
All testing is done without the need to stop your system, avoiding disruption to service.
Find out more…
For more information on our transformer services, download our brochure below. Alternatively, book a consultation, contact us today.